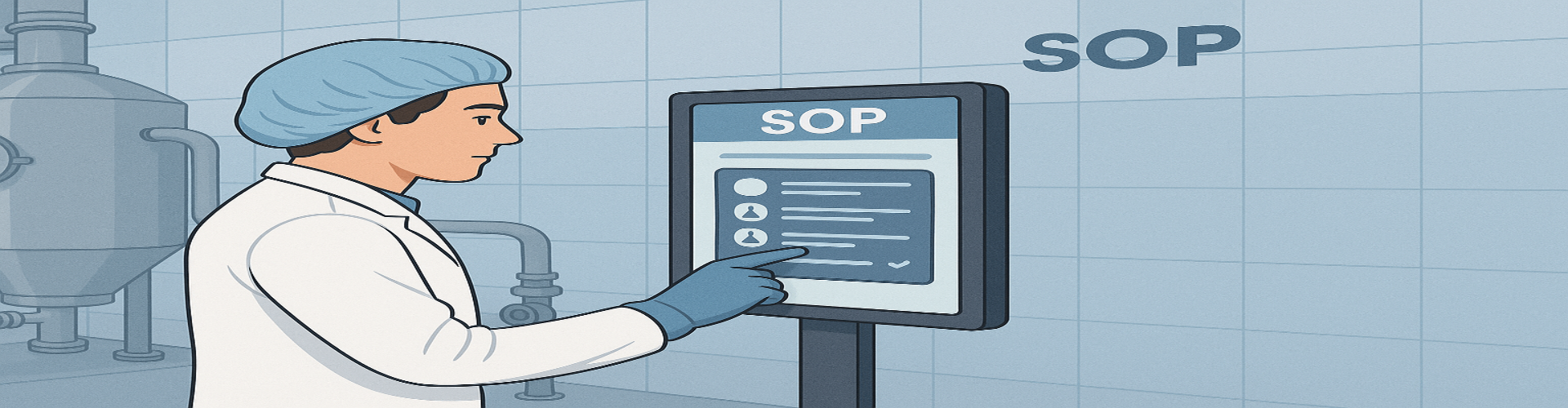
Collaborated with a medical company to improve the SOP (Standard Operating Procedure) process through UX research. The objective was to enhance usability while meeting all QA (Quality Assurance) requirements for operation technicians.
Due to confidentiality, the design process was simplified in compliance with internal regulations.
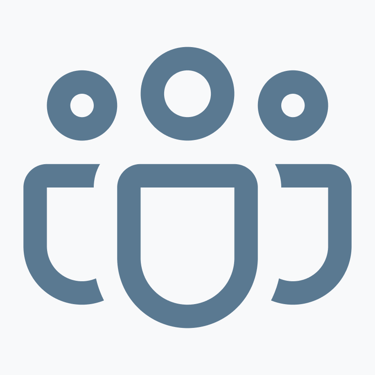
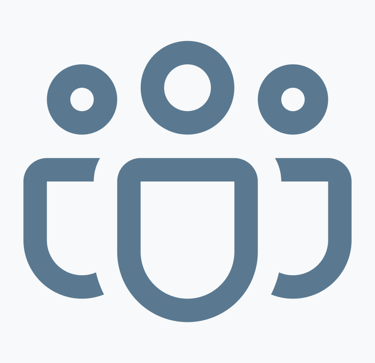
Team
1 UX Researcher
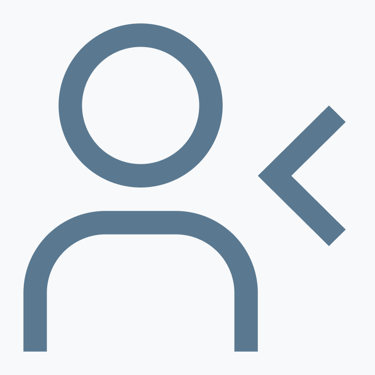
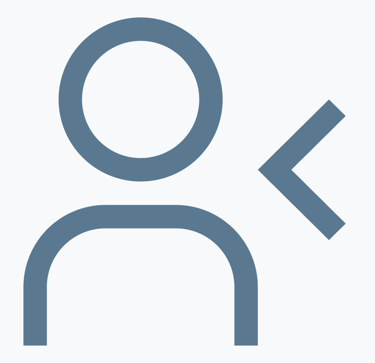
Role
UX Researcher
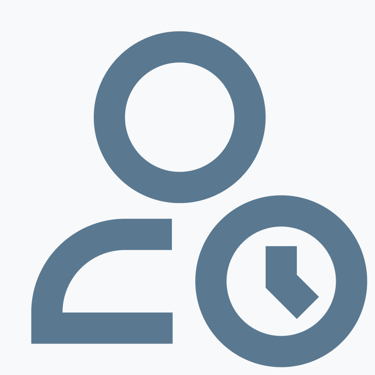
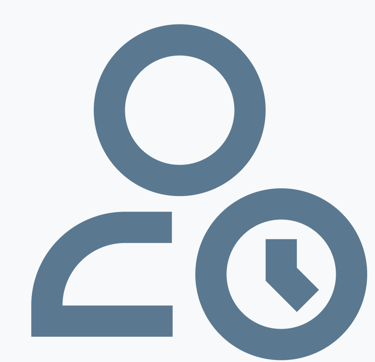
Timeline
4 Weeks
Project Overview
My Role:
As a UX Researcher, I collaborated with a pharmaceutical manufacturing company to improve the clarity and usability of their Standard Operating Procedures (SOPs). I conducted contextual inquiries with technicians on the production floor, interviewed stakeholders across operations and quality assurance, and identified key pain points related to comprehension, navigation, and task execution. My research findings informed the redesign of the SOP interface and content structure, leading to more efficient workflows, reduced errors, and improved compliance with GMP standards.
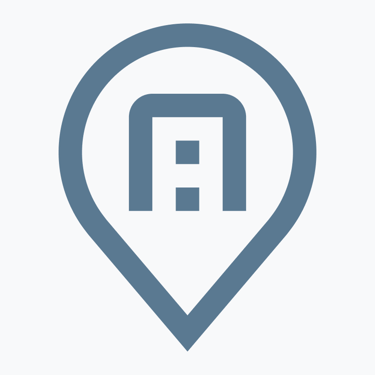
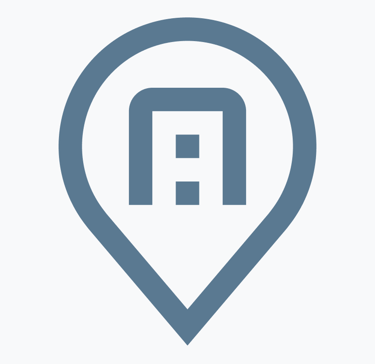
Company
Pharmacutical Company
Target Users
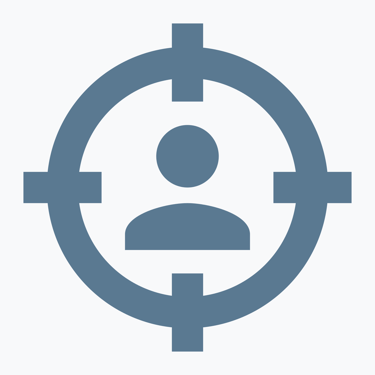
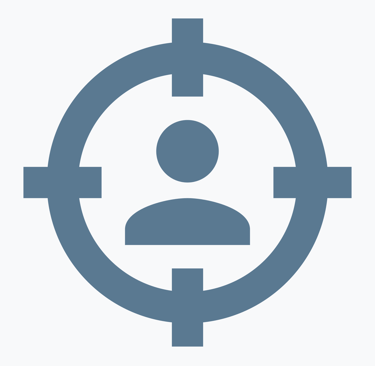
Technicians as a primary user
Quality Assurance (QA) Managers as a secondary stakeholders
Operations / Process Managers as a secondary stakeholders
Perform PCR procedures regularly
Need a clear, error-free workflow and efficient feedback
Oversee protocol compliance and data integrity
Concerned with traceability, accuracy, and minimizing risk
Focus on efficiency, throughput, and resource optimization
Rely on insights from technician workflows to improve productivity
Design Process
I used a double diamond approach based on design thinking methodology. The actions were not linear; we moved between stages as the project advanced.
During the discovery stage, data gathering, observation, and task analysis were conducted to understand the user's pain points and requirements.
In the define stage, the persona was created, and the requirements and needs were documented.
During the development stage, requirements and user needs were integrated into the design solution. The new SOP underwent usability testing and task analysis to ensure it met the requirements effectively.
During the delivery stage, the final version of the SOP was prepared in accordance with company formatting guidelines and subsequently submitted into the system for operational use
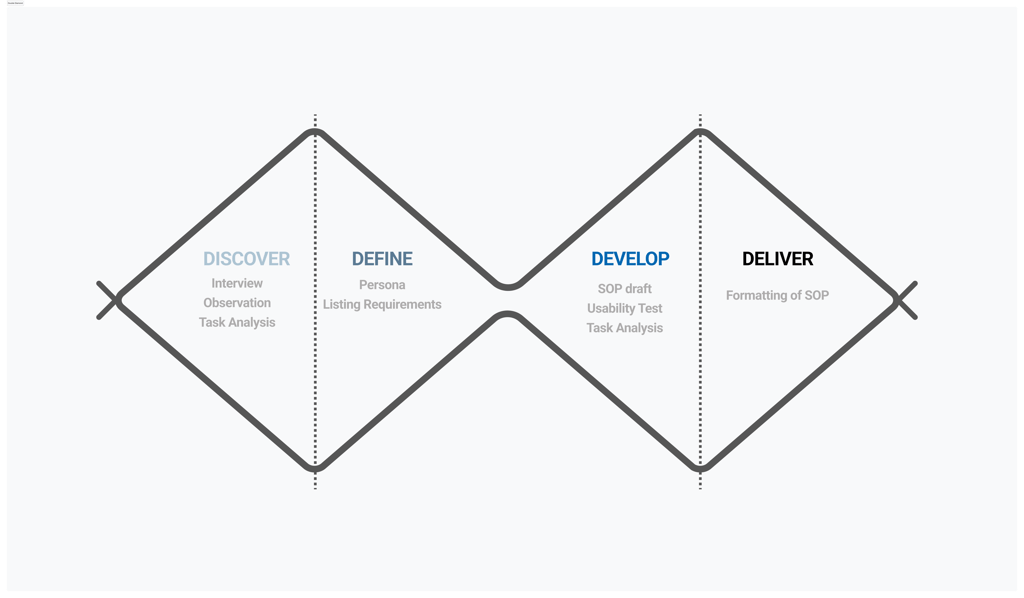
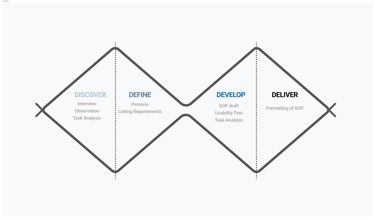
Discover
To understand users and problems, the following steps has been taken:
Stakeholder Interview
Observation in Operation environment
Task Analysis and Usability Testing
Stakeholder Interviews
To begin the project, I conducted in-person interviews with 10 technicians who followed this SOP. Additionally, I interviewed the QA manager and the operations manager.
Interviewing the technicians provided insights into their issues with the SOP, as they are the ones directly interacting with it. Furthermore, speaking with the QA and operations managers allowed me to understand their requirements from both operational and quality assurance perspectives
Observation in operation environment
To understand the technicians' pain points causing confusion and errors, I observed their adherence to the SOP while operating the system. The findings were noteworthy. The steps were not clearly outlined, leading to misunderstandings and varying interpretations. Additionally, the SOP steps were misaligned with operational procedures, especially during shift or operator changes.
Takeaways:
Development technicians found terminology and data entry steps unclear.
The sequence of steps is not aligned with actual operating machine.
Redundant steps caused frustration and errors during setup
Unclear steps caused different interpretation, resulting in confusion, errors.
Task Analysis and Usability testing
Three technicians were instructed to follow part of the SOP and explain their understanding. The results showed varying interpretations, and only one technician managed to perform the step correctly.
Define
After conducting interviews, we identified a user personas : Elena Torres, who works at a pharmaceutical manufacturing facility producing drugs.
Persona
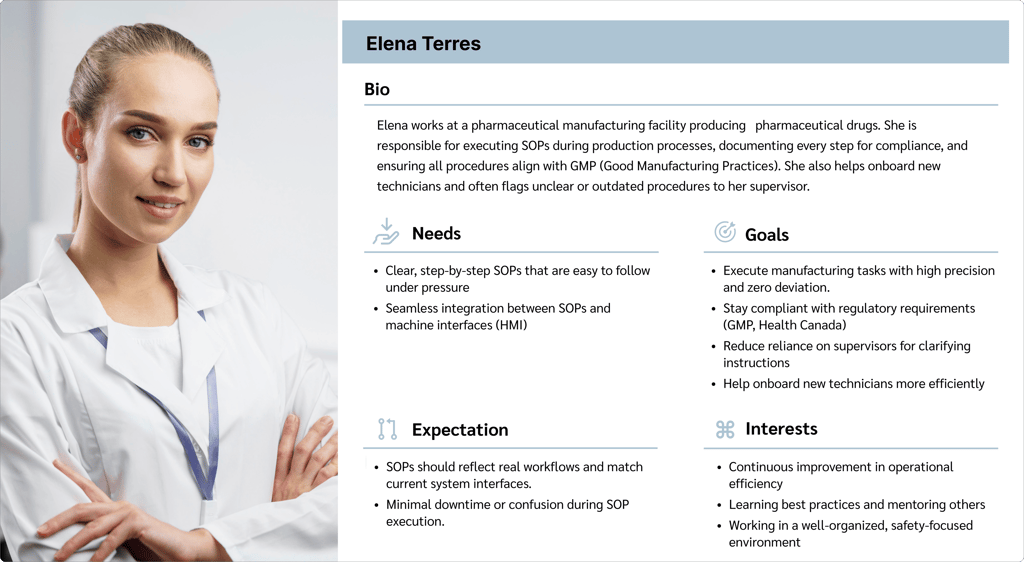

Develop
Design Solutions
After diving deep into all our research data and understanding users' needs and problems, we endeavored to figure out how we could respond to their concerns and address them by incorporating a solution into our design. Here are the possible solutions we came up with:
Challenge 1:
Miss alignment of steps in SOP with operation steps.
Solution 1:
The operation manager and I outlined the steps in the SOP, allowing us to adjust it according to operational needs.
Challenge 2:
Ambiguity in interpreting critical SOP steps
Solution 2:
The senior technician and technician revised the steps to ensure clarity and avoid misunderstandings.
Challenge 3:
Miss alignment of steps in SOP with operation steps.
Solution 3:
The operation manager and I outlined all necessary steps in the SOP, helping to align it with operational needs by adding or removing steps.
Deliver
Usability Test and Task Analysis
After incorporating all design solutions into the SOP, testing showed that over 80% of technicians were satisfied. The new SOP aligned with operations and clarified steps, reducing misunderstandings. Below are some impacts of the new SOP:
The task completion time was reduced from 90 seconds to less than 30 seconds, due to clear steps that minimized the need for questions directed at the senior technician.
Reduced deficiency by 70%
The number of errors decreased from 12 to 5 per run. These remaining 5 errors were due to equipment failures that led to the skipping of some steps in the SOP
Confusion and frustration were significantly reduced among technicians involved in the process.